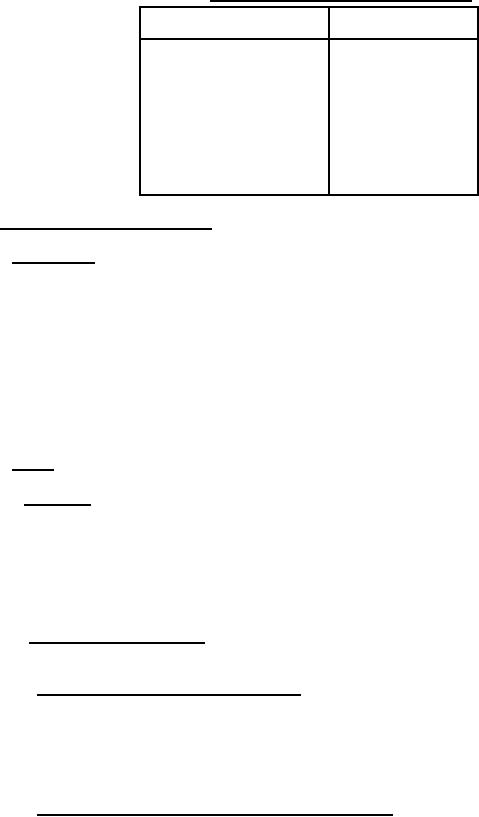
MIL-C-52009D
TABLE I. Examination, zero defect sampling plan.
Lot size
Sample size
1
100 percent
2 -
25
2
26 -
150
8
151 -
500
13
501 - 1,200
20
1,201 - 10,000
32
10,001 - 35,000
50
35,001 - 150,000
80
4.5 Methods of inspection and tests.
4.5.1 Examination. Each control-panel assembly shall be examined as specified herein for the
following defects. Presence of one or more defects shall be cause for rejection:
1.
Dimensions not as specified.
2.
Parts or components missing.
3.
Parts or components misaligned.
4.
Materials or components not as specified.
5.
Wiring and connections not as specified.
6.
Treatment and painting not as specified.
7.
Identification markings not as specified.
8.
Workmanship not as specified.
4.5.2 Tests.
4.5.2.1 Operation. Operate the control-panel assembly from a 115 volt, AC, 60 HZ power source. Set
the autotransformer control dials on 100 volts. Connect two 100 watt, 110/115 volt lamps parallel to any
one of the three circuits controlled by autotransformers. Actuate the master switch to the "ON" position.
Set the appropriate autotransformer control dial to the maximum voltage position and operate for 10
minutes. Measure the output voltage. Reset the control dial to 100 volts. Repeat this test by alternately
applying the lamp load to the other three output circuits. An output voltage of more than 120 volts, or less
than 112 volts, or malfunction of the switch, shall constitute failure of this test.
4.5.2.2. Temperature and humidity. The chambers used for temperature and humidity shall maintain
ambient temperatures within 4°F throughout the test.
4.5.2.2.1 Low temperature storage and operation. Cold soak the control-panel assembly at -50°F for a
period of 12 hours. Test the control-panel assembly at maximum voltage for a period of 1 hour with one
100 watt lamp in each of the four circuits. At the end of each 15 minute period, adjust the
autotransformers from maximum to minimum position and open and close the circuit breaker. Inability of
the control-panel assembly to operate, or malfunction of any component, shall constitute failure of this
test.
4.5.2.2.2 High temperature and humidity storage and operation. Place the control-panel assembly in a
test chamber with 80 to 98 percent relative humidity at an ambient temperature of +155°F for 24 hours;
reduce the temperature to +120°F for 24 hours prior to start of operational tests. Check the circuit
breaker by adjusting the output load to 15 percent overload (5.75amperes) for 1 hour. Increase the
output load to 25 percent overload (6.25 amperes) and determine the time required to trip the circuit
open. Nonconformance to 3.4, damage to the breaker or other components during overload, or
nonconformance to 3.6 shall constitute failure of this test.
5
For Parts Inquires submit RFQ to Parts Hangar, Inc.
© Copyright 2015 Integrated Publishing, Inc.
A Service Disabled Veteran Owned Small Business