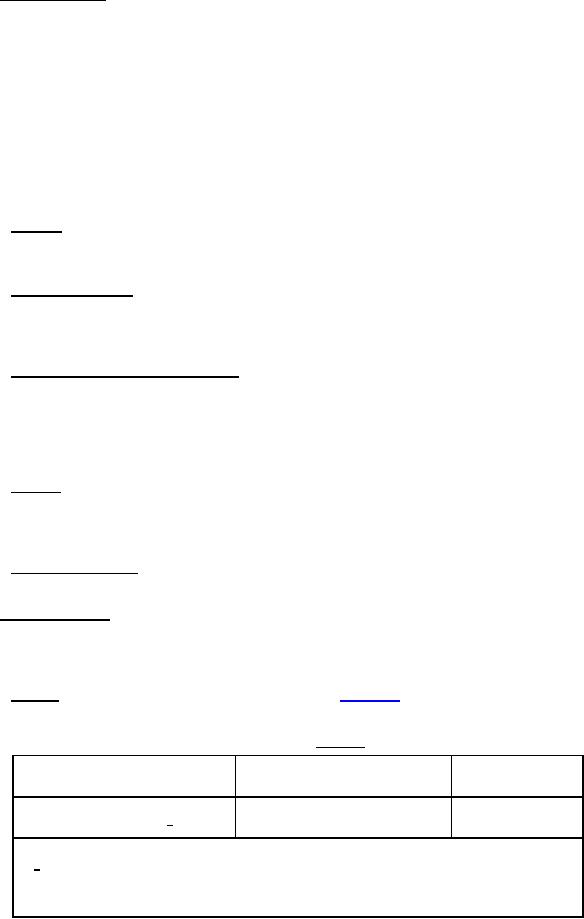
MIL-DTL-917F(SH)
3.7 Treating methods. Most classes of electrical insulation require the use of varnish or other impregnating
compounds to make them satisfactory for service conditions. Without such treatments, the filler materials have
dielectric breakdown values approximately the same as air of the same spacing. In addition, proper treatment seals
out moisture, dust, corrosive atmospheres, and oil vapor. Experience has demonstrated that a thorough treatment
provides essential insurance for satisfactory operation under adverse circumstances. The application of insulating
resin, varnish, or compound to windings and coils may be divided into several different classifications as follows:
a.
Built-up for large coils.
b.
Brushing or flowing initial manufacturing process.
c.
Vacuum-pressure impregnation (VPI) preferred method.
d.
Dipping.
e.
Brushing or spraying (see 3.7.5).
3.7.1 Built-up. By this method, solventless varnish shall be applied by brush between turns as the coil is
wound. This method may be used for deep section coils where other methods cannot ensure complete filling of the
voids.
3.7.2 Brushing or flowing. By this method, varnish shall be applied to the slot portion of preformed coils by
brushing or flowing in order to bond conductors together. Upon curing, this ensures a rigid straight section of the
coil and facilitates the application of the ground insulation. This operation is usually performed only on armature
and stator coils.
3.7.3 Vacuum-pressure impregnation (VPI). By this method, solventless resin shall be applied to a completed
armature or completed stator coil using a VPI cycle. The purpose of this operation is to fill as completely as
possible all voids which exist in the structure and to bond the various parts together. Other types of wound coils
may also be treated by this method. The impregnating solventless resin is introduced into the evacuated treating
vessel or tank without breaking the vacuum seal. After the vacuum cycle is completed, dry air or nitrogen is applied
under pressure to complete the VPI cycle.
3.7.4 Dipping. By this method, varnish shall be applied to the individual winding or coil or to the completed
stator or armature by immersion. The primary purpose of this operation is to fill the interstices of the coil and to
bond the components of the insulation wall together. In addition, a protective coating shall be applied to the surface
of the coil. The hosing or flooding method shall not be used.
3.7.5 Brushing or spraying. Varnish applied to electrical coils by these methods does not ensure complete
impregnation of the internal sections of the coil and, therefore, shall not be used.
3.8 Treating materials. Electrical windings shall be thoroughly treated or impregnated with a material and by a
method which will ensure the evacuation of all air and water from, and the filling in of all interstices within such
windings. The varnish or resin selected shall have such characteristics and be so applied as to ensure thorough
drying, solidification, or curing throughout the innermost recesses of the windings.
3.8.1 Varnish. Varnish shall be selected in accordance with table XIII.
TABLE XIII. Varnish.
Applicable
Application
Type or grade
document
Stationary windings and low
Grade CB, CBH solvent types
MIL-I-24092
speed rotating windings 1/
NOTE:
1/
Low speed windings are defined as 1800 r/min or less, and not more than 24 inches
in diameter. Windings with either a rotational speed greater than 1800 r/min or a
diameter greater than 24 inches are defined as high speed windings.
38
For Parts Inquires submit RFQ to Parts Hangar, Inc.
© Copyright 2015 Integrated Publishing, Inc.
A Service Disabled Veteran Owned Small Business