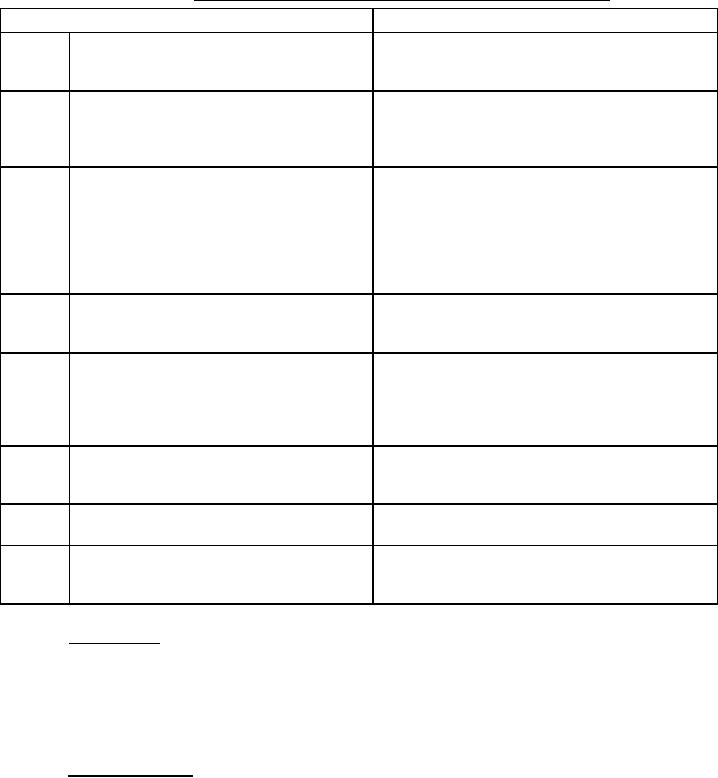
MIL-DTL-917F(SH)
TABLE XIV. Treating guidelines, armature coils, armatures, stators, and field coils.
Dip and bake procedure-solvent varnish
VPI using solventless epoxy resin
Step 1
Ensure that varnish is the correct viscosity and
Ensure that the viscosity and thixotropy index are
solids content is as recommended by the
correct and that the resin has been deaerated.
manufacturer.
Step 2
Prebake the winding to cure the bonding, if
Prebake the winding to cure the armature banding,
used, and to drive off any moisture and
drive off moisture, and to maintain a suitable
volatiles.
temperature for reducing the viscosity of the resin.
Cool to 122 °F (50 °C).
Step 3
Cool to 122 °F (50 °C). Immerse hot coils or
Place the wound unit in the vacuum tank and evacuate
wound apparatus in room temperature varnish
until the desired level of vacuum (5 mm of mercury or
until bubbling ceases or as recommended by
lower) is reached. Allow resin to enter tank without
the various manufacturers.
breaking vacuum seal. Impregnate for ½ hour. Apply
dry air or nitrogen to immersed winding at 90 lb/in2 or
higher for l hour. Reduce pressure, remove winding,
and pump resin back to the storage tank.
Step 4
Drain and air dry for 1 hour. Rotate wound
Drain and air dry for 1 hour. Rotate wound apparatus
apparatus to prevent pocketing the varnish.
while draining (10 minutes) to prevent pocketing the
resin.
Step 5
After draining, but before baking, the metal
After draining, but before baking, the metal surfaces
surfaces of the armature, the bore of the stator,
of the armature, the bore of the stator, and the pole
and the pole faces of the field structure shall be
faces of the field structure shall be wiped with a cloth
wiped with a cloth moistened with solvent.
moistened with solvent. Remove drips and icicles
Remove drips and icicles from winding.
from winding.
Step 6
Bake in circuiting type, forced-exhaust baking
Bake in a circulating type, forced-exhaust baking
oven using a 2-step temperature baking
oven. Rotate to prevent excessive runoff.
schedule.
Step 7
Remove from oven and cool to approximately
Remove from oven and cool to approximately 122 °F
122 °F (50 °C).
(50 °C).
Step 8
Repeat for a total of three treatments,
Repeat steps 3, 4, 5, 6, and 7 as required, reversing the
alternating positions to prevent excessive build
direction of dipping each cycle.
up.
3.10 Final condition. The treated windings and coils shall be clean, smooth, and glossy with good bonding,
filling, and adhesion. Good bonding and adhesion are considered to be achieved when the coil conductors are
secure, firm, and immovable to the touch. More than ½ inch square is considered excessive peeling and the winding
shall be rejected. Bubbles, air pockets, and voids shall be kept to a minimum (treated windings and coils that are
not clean, smooth, and glossy and do not have good bonding, filling, and adhesion shall be subjected to the
insulation suitability test of Appendix A). There shall be no dry (uncoated) spots on the surface. Treated windings
soft and sticky to the touch shall be rejected.
3.11 Insulation suitability. Insulation suitability tests shall be required only on those insulation systems as
specified (see 6.2). The purpose of the test is to determine the insulation resistance, dissipation factor, and
capacitance of an electric winding insulation system under conditions of severe moisture exposure (treated windings
and coils that are not clean, smooth, and glossy and do not have good bonding, filling, and adhesion shall be
subjected to the insulation suitability test of Appendix A). Insulation suitability for electrical windings shall be of
the following types (see Appendix A):
a.
Type CW Complete Winding
b.
Type PW Partial Winding
40
For Parts Inquires submit RFQ to Parts Hangar, Inc.
© Copyright 2015 Integrated Publishing, Inc.
A Service Disabled Veteran Owned Small Business